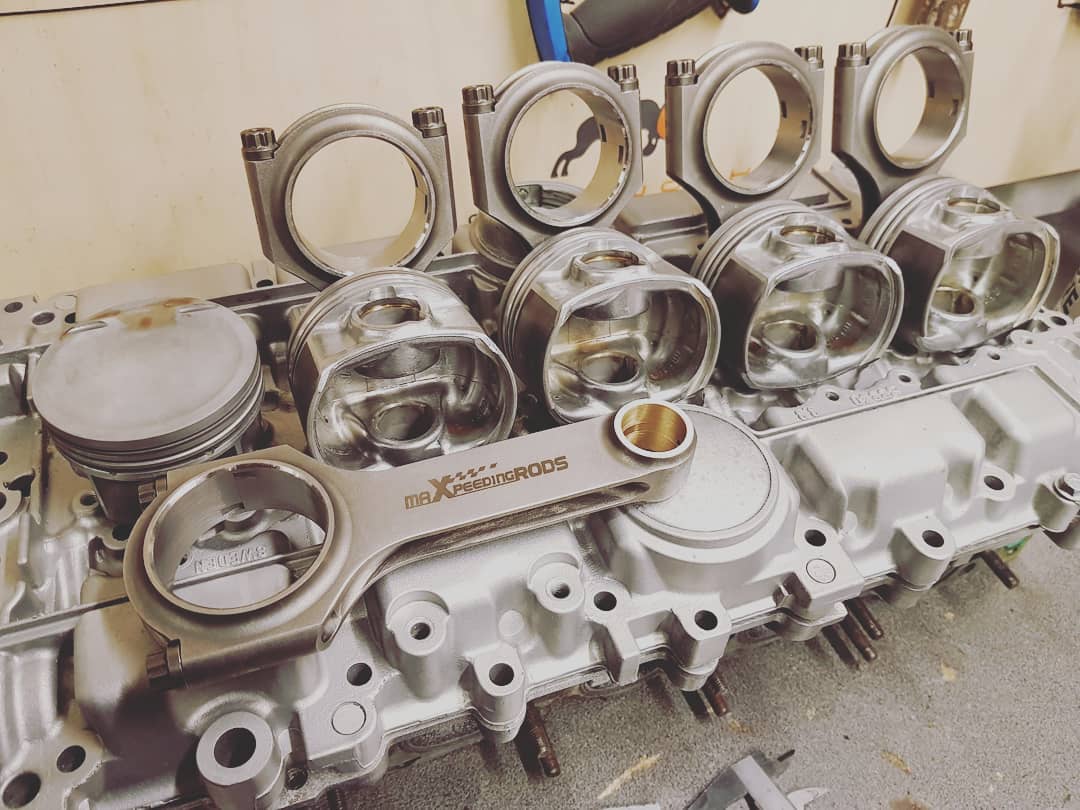
Let’s talk about the most likely parts to fail inside your high-performance engine. This isn’t a talk many enthusiasts like to have, but it’s a necessary one. When an automotive engine is pushed to its limits, failure is a real possibility. What parts are put at the highest stress? What components are usually guilty of not measuring up?
Usually, valve springs are the first to go. Most enthusiasts are guilty of revving their engines beyond the capability of their springs, and they experience valve float. The spring is not able to close the valve fast enough, or the spring can break from being overstressed. Either way, it’s no longer capable of doing its job, and the valve does not close before it makes contact with the piston. The results are never good.
Next, we’re probably looking at rod bearings. This is almost always the result of something else, but the connecting rod bearings are under such a great load, the bearings will fail first. This is usually the result of either inadequate oil pressure or improper clearances between the bearing and the crankshaft journal. Either way, the bearing fails, and the delicate balance between clearance, oil pressure, and heat is thrown out of whack. The resulting damage is directly relevant to how quickly the driver realizes something is not right and shuts the engine down. If it’s allowed to continue spinning the heat will eventually cause the rod to fail, sending it into a collision course with the crankshaft and possibly evicting it from the block entirely.
Finally, we’re down to the connecting rod itself. Even when the rod bearing clearance is correct and oil pressure is adequate for the rpm level, the stresses on the connecting rod can cause it to fail. The rod must be designed well, balanced properly, and not overstressed from the pressures put upon it by either cylinder pressure loads from the piston or the stresses of high rpm operation. Its materials must be of premium quality, without flaws or inconsistencies. Its machining must be impeccable, with the upper and lower portions of the rod fitting together as if they were one. The hardware holding the two parts together must be of premium quality and have to be installed properly, lubricated properly, and stretched properly (and consistently) through proper tightening and torque methods.
If any one of these factors is not correct, the connecting rod is susceptible to failure in a high-performance application. Consider not just the stresses of making big power, but also the high temperatures the rod must face, and the incredible task of changing speeds in an instant, being put under heavy loads, unloading immediately, and then being forced to change direction at such a high rate (from going one way, to then going completely in the opposite direction) under a high load and at incredible speeds.
This is why high-performance engines demand that the connecting rods be forged, or of billet construction. Its why balancing is so critical, and it’s why the machining processes must be of the highest quality.
If you’re an engine enthusiast, you’ll know that some companies built their entire reputation on designing and manufacturing connecting rods for racing engines. The need is so great, that if reliable, durable parts could be had, they could be sold at a premium rate. Add more features to that list, like custom lengths, custom piston pin diameters, and custom rod end sizing, and you’ll see how specialized production of high-performance connecting rods can be a demanding business.
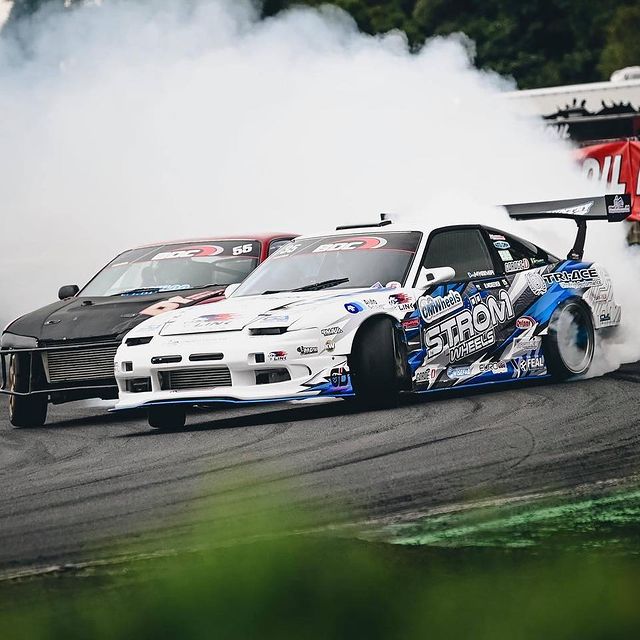
Racers are fickle. If your parts experience failures, we are always quick to jump in and offer replacements to customers. We keep quality at its highest level at all times. It’s not an easy thing, but it’s worth it.
Like all high-performance rods, these rods are crafted from 4340 forged steel, and they go through a multi-stage heat treatment process to gain resistance to fatigue. Then, they are shot-peened and micro-polished to eliminate all sharp edges and stress risers where cracks could potentially form. Finally, they are titanium-plated (a process they call tetanizing) to provide a strong surface layer that both resists bending a bit more and helps shed oil off the surface of the rod at high rpm.
The H-beam design rods are CNC-machined to their final dimensions to ensure consistency, and the bores are honed to precise tolerances. They are fitted with bronze wrist pin bushings to increase wear resistance and hold lubricant. The rods are optimally balanced within 1 gram and are drilled for pin oiling.
Then, they go through a rigorous quality assurance process, which includes magnafluxing to inspect for any flaws or nicks in the surfaces. The parts are then X-ray tested to ensure the quality of the forging and verify there are no flaws. Finally, they are sonic-tested to guarantee consistency and quality.
This is how high-performance connecting rods are crafted. Because of our commitment to quality, the product rivals other competing forged rods for strength and durability.